编者 过定位容易造成基准变动,后面用图补充说明了。 本来定位点A和B已经定义了一条AB基准,批量加工时,所有零件的尺寸都是在这个基准上围绕某个中间值做分布(想想正态分布)。硬要加入一个C点的话,会出现三个线基准:AB、AC、BC;实际加工时,不会知道是哪条基准线起作用,有可能是1条,有可能是2条,也有可能是3条。 如果只有一条基准线起作用,那多出的那个点就没有起到定位作用,你以为是过定位,实际上没有过定位。如果有2条或者3条基准线起作用,那么一批零件的尺寸会在不同的基准上围绕不同的中间值分布,基准与基准之间一定是有差距的(也许这个差距很小很小),那么这批零件尺寸的分布范围就人为的扩大了,尺寸误差范围扩大,这就是我们所说的影响工件精度。举个车削例子具体看下图(很渣): 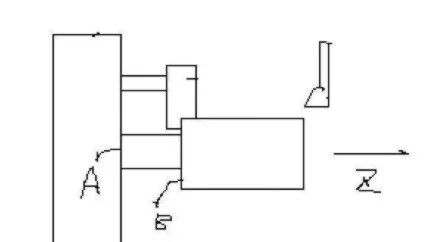
# [# d9 L1 g; j. e9 W+ p) Z& m​0 R& F* C8 l( X1 J: X2 g& s
车削这个圆柱形零件,Z方向的定位,要么拿零件端面A做基准,要么拿轴肩B面做基准,如果两个基准都用,Z方向就会出现过定位情况。零件尺寸分布就会有A分布和B分布。A分布的期望和B分布的期望肯定是有差值的,这个差值就会导致这批零件尺寸分布扩大,误差增大。 定位这个概念暗含了一个假设前提:被定位物体是个刚体(运动中和受力作用后,形状和大小不变,而且内部各点的相对位置不变的物体)。但实际上,机械加工中都是弹性体,在自身重力和切削力作用下,会变形,会振动,导致被加工件刚性不足。这时我们会用过定位的方式来弥补这种不足。看下图(更渣) , d% T, o R2 p
​
7 r: ^5 b9 b) {长轴类零件车削时,从理论上讲零件在卡爪处已经被定位并夹紧了,但不用顶尖的话,尾端加工会振刀,即使不加工,本身的旋转就跟甩葱一样。顶尖孔是锥孔,这个锥孔的定位和卡爪处的定位都作用在一个零件上,这个零件实际自转轴就难确定。但是这个误差产生的影响远远远远小于这个零件不用顶尖的影响,后者甚至都无法完成加工。车削怕轴,谁干谁知道。 还有大家要区分定位和夹紧的概念,定位目的是确定空间位置,约束自由度,夹紧是为了保证这个空间位置(这些被约束的自由度)在加工过程中不变化。这都是针对刚体这个概念而来的。但零件实际上都是弹性体,由于夹持力过大导致零件变形,影响加工精度,是另外的问题了。 |