本帖最后由 twq19810302 于 2023-4-3 13:44 编辑 % }. g4 K& g/ g$ O7 g+ E! U5 i' K+ Q
% _! [/ E/ _( U在我们的生活中轴承几乎无处不在,小到路边的共享单车、家里的家用电器,大到上天的宇宙飞船,下水的航空母舰,没有轴承这一切都无法存在。 $ Z! ?/ |$ y& \
然而应用于高精密机械的主轴承,我国在技术上仍处于一片空白。 - M% {! L W2 D+ C* P
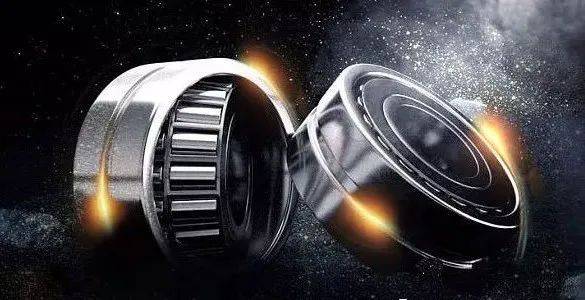 滚动轴承的精度一般分为P0、P6、P5、P4和P2五个等级,用于精密机床主轴上的轴承精度应为P5及以上级。而对于数控机床、加工中心等高速、铁路、航空等高科技领域,则需选用P4及以上级超精密轴承,P4及以上级超精密轴承对技术性能和可靠性要求很高,国内需求的一半以上都依赖进口。 0 F" b7 O7 I( V5 H: B
而造成国产轴承与进口轴承产生较大质量差距,主要原因如下:
! ~; `; t- R5 G# J7 j& B+ X
01 轴承成品质量差异 国内外大量试验表明:保持架、套圈、钢球的加工质量对轴承振动具有不同程度的影响,其中钢球的加工质量对轴承振动影响最明显,其次是套圈的加工质量,最主要影响因素是钢球和套圈的圆度、波纹度、表面粗糙度、表面磕碰伤等。 我国钢球产品最突出的问题是振动值离散大,表面缺陷严重(单点、群点、凹坑等),尽管表面粗糙度、尺寸、形状、误差都不低于圈外水平,但合套后轴承振动值高,甚至产生异音,主要问题是波纹度没有控制(无标准、无合适测试分析仪器),同时说明机床的抗振性差,砂轮、研磨盘、冷却液、工艺参数均存在问题;另一方面要提高管理水平,避免磕碰伤、划伤、烧伤等随机性质量问题。 对于套圈,影响轴承振动最为严重的也是沟道波纹度和表面粗糙度。例如,中小型深沟球轴承内外沟道圆度大于2μm时,将对轴承振动产生明显影响,内外沟道波纹度大于0.7μm时,轴承振动值随波纹度增加而增加,沟道严重磕伤可使振动上升4dB以上,甚至出现异音。
# ~8 t x) a: l0 N" g% z
0 J# j" g) h2 p. k
02 生产流程、人才等拉开距离 1.工业技术的差距。轴承技术工人,乃至工程师的社会地位得不到应有的尊重(近年来这种情况有了很大改观)。我国教育产业发展不均衡,技术教育没有得到应有的重视,导致年轻人宁做白领无所事事,也不愿意工作在生产一线。同时也导致了国内现今人人创业,而大多小微轴承工厂、轴承公司没有高质量技术人员,只能生产一些没有竞争力的低端轴承产品。 2.材质上的差距。世界钢铁看中国,中国钢铁看河北,但是这仅仅指的是粗钢产量,这也是近年来世界经济下滑,国内钢铁产能过剩,钢铁价格一直萎靡不振的一个原因。合金钢一直就是国内钢铁产业的短板,高端冶金技术又是发达国家对我们严格保密的,加上国内钢企研发上的不足,造成了我国轴承乃至工业技术的先天性的不足。 3.生产工艺的差距。在这里,我只讲述一下自己的想法。生产工艺是工业技术里最重要的环节,是一个循环往复,量变产生质变的过程。以机床为例,轴承对机床的精度有巨大的影响,高端精密轴承的大客户群体就是机床主轴轴承。而国产精密轴承的寿命、精度与国外轴承有着巨大的差距。 4.生产设备差距。轴承厂家与应用厂家是鱼与水的关系。没有好的轴承,生产不出好的设备,没有可靠的机床加工不出高质量的轴承。据我所知大型的机加工厂家采购的基本都是进口机床。而国内一些实力较小的轴承厂家宁可采购上世纪的老式机床改造成轴承加工专用机床,也不愿采购国内知名品牌的机床。这其中有价格因素,也有实用性的因素。 5.没有有力的支持者。近年来我国高铁技术快速发展,但是高速铁路轴承却采购自德国舍弗勒集团。究其根本原因,在部分领导的操纵下西北轴承厂舍弗勒开始了合作。但是在几年的合作过程中,西北轴承厂没有得到应有的技术支持,还丧失了大量的市场份额,导致今天西北轴承的式微。
2 n& B, w# z% z; s8 W) {
在我们的生活中轴承几乎无处不在,小到路边的共享单车、家里的家用电器,大到上天的宇宙飞船,下水的航空母舰,没有轴承这一切都无法存在。 然而应用于高精密机械的主轴承,我国在技术上仍处于一片空白。 2 f3 e! Z$ |0 F& K$ q
滚动轴承的精度一般分为P0、P6、P5、P4和P2五个等级,用于精密机床主轴上的轴承精度应为P5及以上级。而对于数控机床、加工中心等高速、铁路、航空等高科技领域,则需选用P4及以上级超精密轴承,P4及以上级超精密轴承对技术性能和可靠性要求很高,国内需求的一半以上都依赖进口。
+ m, n* p9 i0 _) d# J/ `
而造成国产轴承与进口轴承产生较大质量差距,主要原因如下: 7 R+ I9 p, [& L$ E9 k) ^; p& n- C" z
01 轴承成品质量差异 国内外大量试验表明:保持架、套圈、钢球的加工质量对轴承振动具有不同程度的影响,其中钢球的加工质量对轴承振动影响最明显,其次是套圈的加工质量,最主要影响因素是钢球和套圈的圆度、波纹度、表面粗糙度、表面磕碰伤等。 我国钢球产品最突出的问题是振动值离散大,表面缺陷严重(单点、群点、凹坑等),尽管表面粗糙度、尺寸、形状、误差都不低于圈外水平,但合套后轴承振动值高,甚至产生异音,主要问题是波纹度没有控制(无标准、无合适测试分析仪器),同时说明机床的抗振性差,砂轮、研磨盘、冷却液、工艺参数均存在问题;另一方面要提高管理水平,避免磕碰伤、划伤、烧伤等随机性质量问题。 对于套圈,影响轴承振动最为严重的也是沟道波纹度和表面粗糙度。例如,中小型深沟球轴承内外沟道圆度大于2μm时,将对轴承振动产生明显影响,内外沟道波纹度大于0.7μm时,轴承振动值随波纹度增加而增加,沟道严重磕伤可使振动上升4dB以上,甚至出现异音。 4 b9 U( T7 V# A$ l+ B& C
02 生产流程、人才等拉开距离 1.工业技术的差距。轴承技术工人,乃至工程师的社会地位得不到应有的尊重(近年来这种情况有了很大改观)。我国教育产业发展不均衡,技术教育没有得到应有的重视,导致年轻人宁做白领无所事事,也不愿意工作在生产一线。同时也导致了国内现今人人创业,而大多小微轴承工厂、轴承公司没有高质量技术人员,只能生产一些没有竞争力的低端轴承产品。 2.材质上的差距。世界钢铁看中国,中国钢铁看河北,但是这仅仅指的是粗钢产量,这也是近年来世界经济下滑,国内钢铁产能过剩,钢铁价格一直萎靡不振的一个原因。合金钢一直就是国内钢铁产业的短板,高端冶金技术又是发达国家对我们严格保密的,加上国内钢企研发上的不足,造成了我国轴承乃至工业技术的先天性的不足。 3.生产工艺的差距。在这里,我只讲述一下自己的想法。生产工艺是工业技术里最重要的环节,是一个循环往复,量变产生质变的过程。以机床为例,轴承对机床的精度有巨大的影响,高端精密轴承的大客户群体就是机床主轴轴承。而国产精密轴承的寿命、精度与国外轴承有着巨大的差距。 4.生产设备差距。轴承厂家与应用厂家是鱼与水的关系。没有好的轴承,生产不出好的设备,没有可靠的机床加工不出高质量的轴承。据我所知大型的机加工厂家采购的基本都是进口机床。而国内一些实力较小的轴承厂家宁可采购上世纪的老式机床改造成轴承加工专用机床,也不愿采购国内知名品牌的机床。这其中有价格因素,也有实用性的因素。 5.没有有力的支持者。近年来我国高铁技术快速发展,但是高速铁路轴承却采购自德国舍弗勒集团。究其根本原因,在部分领导的操纵下西北轴承厂舍弗勒开始了合作。但是在几年的合作过程中,西北轴承厂没有得到应有的技术支持,还丧失了大量的市场份额,导致今天西北轴承的式微。 7 I+ E" |; U1 u
03 高端轴承应用的空白 与国外相比,国产轴承在高端和大型轴承方面存在较大差距,主要行业为: 01 航空方面 作为航空发动机的关键基础零部件,国外正在研发推力比为15-20的第2代航空发动机轴承,准备在2020年前后装配到第5代战机中。近10年来,美国研发了第2代航空发动机用轴承钢,其代表性钢种为耐500℃的高强耐蚀轴承钢CSS-42L和耐350℃高氮不锈轴承钢X30(Cronidur30),中国则在进行第2代航空发动机用轴承的研发。 02 汽车方面 对于汽车轮毂轴承,中国目前广泛应用的是第1代和第2代轮毂轴承(球轴承),而欧洲已广泛采用第3代轮毂轴承。第3代轮毂轴承的主要优点是可靠、有效载荷间距短、易安装、无需调整、结构紧凑等。目前,中国引进车型大多采用这种轻量化和一体化结构轮毂轴承。 03 铁路车辆方面 目前,中国铁路重载列车用轴承采用国产电渣重熔G20CrNi2MoA渗碳钢制造,而国外已经将超高纯轴承钢(EP钢)的真空脱气冶炼技术、夹杂物均匀化技术(IQ钢)、超长寿命钢技术(TF钢)、细质化热处理技术、表面超硬化处理技术和先进的密封润滑技术等应用到轴承的生产和制造,从而大幅度提升了轴承的寿命与可靠性。中国电渣轴承钢不仅质量低,而且成本比真空脱气钢高出2000-3000元/吨,未来中国需要开发超高纯、细质化、均匀化与质量稳定的真空脱气轴承钢取代目前采用的电渣轴承钢。 04 风电能源方面 对于风电轴承,目前中国还无法生产技术含量较高的主轴轴承和增速器轴承,基本依靠进口,3MW以上风电机组配套轴承的国产化问题还没有解决。国外为了提高风电轴承的强度、韧性和使用寿命,采用了新型特殊热处理钢SHX(40CrSiMo),对于偏航和变浆轴承,通过表面感应淬火热处理控制淬硬层深度、表面硬度、软带宽度和表面裂纹。对于增速器轴承和主轴轴承采用碳氮共渗,使零件表面得到较多稳定残余奥氏体体积分数(30%-35%)和大量细小碳化物、碳氮化物,提高了轴承在污染润滑工况下的使用寿命。
1 a# }* z1 T- z! W
04 未来国产轴承改善方向
& @9 F+ a* K4 \' J- O5 ~( Q
主要体现在四个方面改善: 01. 轴承钢洁净度 在考虑经济性的前提下,进一步提高钢的洁净度,降低钢中的氧和钛含量,达到轴承钢中的氧与钛的质量分数分别小于6×10-6和15×10-6的水平,减小钢中夹杂物的含量与尺寸,提高分布均匀性。 02 组织细化与均衡化 通过合金化设计与控轧控冷工艺的应用,进一步提高夹杂物与碳化物的均匀性,降低和消除网状和带状碳化物,降低平均尺寸与最大颗粒尺寸,达到碳化物的平均尺寸小于1μ m的目标;进一步提高基体组织的晶粒度,使轴承钢的晶粒尺寸进一步细化。 03 减少低倍组织缺陷 进一步降低轴承钢中的中心疏松、中心缩孔与中心成分偏析,提高低倍组织的均匀性。 04. 轴承钢的韧性 通过新型合金化、热轧工艺优化与热处理工艺研究,提高轴承钢的韧性。 与国外相比,国产轴承在高端和大型轴承方面存在较大差距,主要行业为:
0 ?1 P- c! s {5 [8 C7 o" Q, e9 @8 @
01 航空方面 作为航空发动机的关键基础零部件,国外正在研发推力比为15-20的第2代航空发动机轴承,准备在2020年前后装配到第5代战机中。近10年来,美国研发了第2代航空发动机用轴承钢,其代表性钢种为耐500℃的高强耐蚀轴承钢CSS-42L和耐350℃高氮不锈轴承钢X30(Cronidur30),中国则在进行第2代航空发动机用轴承的研发。
+ I( Q/ r6 q; y* M; u( [
02 汽车方面 对于汽车轮毂轴承,中国目前广泛应用的是第1代和第2代轮毂轴承(球轴承),而欧洲已广泛采用第3代轮毂轴承。第3代轮毂轴承的主要优点是可靠、有效载荷间距短、易安装、无需调整、结构紧凑等。目前,中国引进车型大多采用这种轻量化和一体化结构轮毂轴承。
7 y ]0 I) M7 \0 f, W, D' b
03 铁路车辆方面 目前,中国铁路重载列车用轴承采用国产电渣重熔G20CrNi2MoA渗碳钢制造,而国外已经将超高纯轴承钢(EP钢)的真空脱气冶炼技术、夹杂物均匀化技术(IQ钢)、超长寿命钢技术(TF钢)、细质化热处理技术、表面超硬化处理技术和先进的密封润滑技术等应用到轴承的生产和制造,从而大幅度提升了轴承的寿命与可靠性。中国电渣轴承钢不仅质量低,而且成本比真空脱气钢高出2000-3000元/吨,未来中国需要开发超高纯、细质化、均匀化与质量稳定的真空脱气轴承钢取代目前采用的电渣轴承钢。
/ ^2 Q: d! J! l/ d& R7 W. u I
04 风电能源方面 对于风电轴承,目前中国还无法生产技术含量较高的主轴轴承和增速器轴承,基本依靠进口,3MW以上风电机组配套轴承的国产化问题还没有解决。国外为了提高风电轴承的强度、韧性和使用寿命,采用了新型特殊热处理钢SHX(40CrSiMo),对于偏航和变浆轴承,通过表面感应淬火热处理控制淬硬层深度、表面硬度、软带宽度和表面裂纹。对于增速器轴承和主轴轴承采用碳氮共渗,使零件表面得到较多稳定残余奥氏体体积分数(30%-35%)和大量细小碳化物、碳氮化物,提高了轴承在污染润滑工况下的使用寿命。
: B7 m% G& i: q. y/ t
04 未来国产轴承改善方向 $ p1 ]# @! W/ @; i7 B) A
主要体现在四个方面改善: 01. 轴承钢洁净度 在考虑经济性的前提下,进一步提高钢的洁净度,降低钢中的氧和钛含量,达到轴承钢中的氧与钛的质量分数分别小于6×10-6和15×10-6的水平,减小钢中夹杂物的含量与尺寸,提高分布均匀性。 02 组织细化与均衡化 通过合金化设计与控轧控冷工艺的应用,进一步提高夹杂物与碳化物的均匀性,降低和消除网状和带状碳化物,降低平均尺寸与最大颗粒尺寸,达到碳化物的平均尺寸小于1μ m的目标;进一步提高基体组织的晶粒度,使轴承钢的晶粒尺寸进一步细化。 03 减少低倍组织缺陷 进一步降低轴承钢中的中心疏松、中心缩孔与中心成分偏析,提高低倍组织的均匀性。 04. 轴承钢的韧性 通过新型合金化、热轧工艺优化与热处理工艺研究,提高轴承钢的韧性。
5 I" [: ^6 p8 t8 h# d } |