|
数控机床床身在铸造和机械加工等工艺过程中,由于受热或受力不均匀,其内部都会产生不同程度的残余应力。残余应力的存在,极大地影响了机床床身的尺寸稳定性、刚度、强度和机械加工性能等,严重影响着机床的装配和正常使用。振动时效技术是继热时效和自然时效后的一项环保型新技术。基本思想是通过对应力工件施以循环载荷,使工件内应力释放,从而使工件残余应力降低,达到时效之目的。
0 n7 s p; A, H0 i% Q: u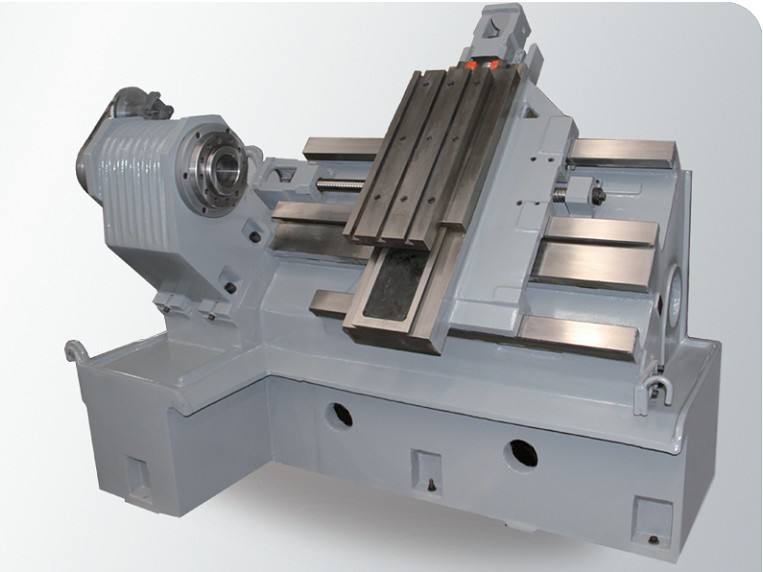
1 f2 B3 a" W1 T {5 W0 ^; ? ( {/ a8 ~+ S. {% t- e8 P
本文针对大型数控机床床身的特点,进行了大型数控机床床身振动时效机理、振动时效工艺和振动时效效果的研究,得到了大型数控机床床身振动时效工艺的工艺规范,提高了机床床身的尺寸稳定性、刚度、强度和机械加工性能等。
4 o f- S& R% g/ `) R5 n
. g7 L2 s1 c' ~) E8 _ 1 数控机床床身振动时效机理
& H5 J5 \: g) L# ~* t! N% p 3 E E4 H1 w4 I R
从材料的应力应变特性角度分析。工程上采用的材料都不是理想的弹性体,其内部存在着不同类型的微观缺陷,铸铁中更是存在着大量形状各异的切割金属基体的石墨,其中的微观缺陷附近都存在着不同程度的应力集中。振动时效消除残余应力的必要条件是动应力(激振力)和残余应力之和大于材料的屈服极限。
# u: _, E2 a9 @$ N在工件内残余应力的高峰值处将产生局部屈服,引起微小塑性变形,使得工件内部残余应力高峰值降低和残余应力重新均匀分布,使工件内原来不稳定的残余应力得到松弛和匀化;同 时,由于包辛格效应,经过一段时间循环后,工件的屈服极限上升,直到与所受应力相等,工件内部不再产生新的塑性变形,工件的弹性性能得到强化,金属基体达到强化,增强了抗变形能力,提高了工件尺寸精度稳定性。$ y S8 k/ u# n X3 o
. t2 J! J" H0 }
机床床身的应力集中区,绝大部分是在工件的微观缺陷区,如位错、空位、夹杂等,引起金属内缺陷区大量位错移动。位错滑移一开始就相当于晶体开始屈服,工件的自变形就是位错滑移的结果。如果有某种方式使易动位错先滑移,余下位错不易滑移,其最终结果就可减少构件的自变形使尺寸稳定。位错运动一方面产生位错增殖及亚结构的变化;另一方面使晶体产生微观塑性变形。位错增殖及亚结构的变化将使金属发生强烈的加工硬化,即继续塑性变形的抗力增大,强度大大提高,从而提高工件抗变形能力和尺寸稳定性。而金属晶体的微观塑性变形将使高残余应力得以释放,消除或降低应力集中,达到均化应力的目的。
8 L; r( e! ?% a8 ~6 n0 c0 J 从以上分析可知:当工件受到动应力的作用时,在其内部激起局部应变,应力集中越大的区域产生的应变也越大,结果耗掉了应力峰值,使应力均化并降低。5 h2 {% J! l+ N( q" L
4 Q% C @ `/ o8 z, Y0 l 2数控机床床身振动时效工艺 - L: ^% r/ O* B( {! G. _. f+ r. i
) V4 x6 ]1 D' c9 \6 L5 _ 振动时效的大型数控机床床身特点如下:& g2 C; N( j; B0 U2 f/ j
(1)其机床床身的结构较长;& @( j, j7 l4 n& D, ^5 r
(2)机床床身内部的加强筋较多;
- u7 z% L, D5 \2 Q(3)机床床身在铸造过程中,导轨面朝下,浇注口和冒口在两端;
2 b8 r# x7 b% L8 \4 V# W- q9 h(4)由于机床床身铸造后变形量较大,则铸造时给粗加工留有较大的加工余量。数控机床的床身为铸件,由于机床床身在铸造及粗加工后,存在有残余应力,且残余应力不稳定性,造成应力松弛和应力的再分布,使工件产生变形,影响机床精度,因此需要在粗加工后进行振动时效处理消除残余应力。
. @' _4 V! \" H0 p5 F r" A' V振动时效是基于谐波共振原理。在振动时效过程中工件处在外部激振器激振力的持续作用下,零件处于“受迫振动”时的一个特殊状态,即在激振器所产生的周期性外力的作用下使零件产生共振,从而使工件的残余应力得到部分消除和均布,从而达到时效的目的。
7 C" i, ~4 ^6 n$ t K: q$ `- [
+ ~( \5 J o) I- O
6 A8 U6 z: A3 \7 V/ ]; KHK振动时效消除机床导轨应力 3 I2 u% q% j: G ]1 i0 `8 S# T4 P
3 Z5 N3 b4 B: u" \+ \9 t; p( J振动时效工艺方案的确定包括以下6个方面的内容: (1)支撑点的选择; (2)激振点的选择; (3)传感器安放位置; (4)主振频率的确定; (5)激振力的大小; (6)振动时间的确定。
$ y9 d4 t7 @! N1 A q ~% m( F; [1 H) v4 v% \9 q8 N) w0 a/ U- t
2.1支撑点的选择
, R1 L$ J# |. o, G7 s 机床床身的支撑选用4个橡胶垫作支撑,支撑点选择在机床床身振动的节线处。选择节线处作支撑点,以避免零件和支撑物在振动时因相互撞击而消耗能量和产生噪音,同时可以减小能量,获得较大的振幅。其方法是在振动时,在机床床身的导轨面上抛撒砂子,砂子聚集处位置为节线位置,将位置作为支撑点。 ! R+ P* c' B3 O% s8 G$ a* ~
2 G9 \. l6 M( C0 ^+ R2 P0 `1 G
2.2 激振点和传感器位置选择
' X* M6 s" x A: ]" B) p T 当对工件进行振动时,其振动值最大处称为波峰。激振器夹持在工件波峰处,这样激振器即可以最小能量激发工件产生较大振动。传感器放置在另一波峰处有利于振动信号的拾取,因为传感器所拾取的信号一般需经放大器放大后才能进行后续处理。图1所示是将激振器刚性地固定在床头箱部位一边的波峰处,传感器固定在远离激振器且振幅较大的床身靠端部的平面导轨上 0 r7 `$ P: {; w0 j
# l5 a/ c/ |+ q/ v
2.3 主振频率的确定 5 m$ c7 o$ ~# r
激振频率的选择与工件本身的形状、重量、材质和刚性等因素有关。机床床身的固有频率用振动时效设备的扫频功能来确定。在扫频的过程中,工件有时候会出现几个共振峰。在一般情况下,时效处理应选择在一阶亚共振区进行,亚共振区是指一阶共振峰的前沿,即最大加速度值的1/3~2/3处,这一点的频率就是振动主频率,这样不会对工件造成疲劳损伤,相反还会提高工件的疲劳寿命。
% a3 B, H t, v# j
: r K# ]; O, O2 m4 s- S5 |+ s; c 2.4激振力的确定
8 a% U6 R- K o0 N+ \4 R; c 激振力的大小通过调节偏心距e获得,所以振动时效是简谐激励下的受迫振动。机床床身内部动应力的大小除与激振力的大小有关外,还与振型、频率等有关,即与机床床身的刚度和振动时的支撑状态有关,也就是说当激振频率和振型为机床床身的某价固有频率和振型时,才可以发生共振,获得较大振幅,相应的动应力也较大,降低残余应力的效果也较好。根据振动时效机理,确定激振力大小的原则是激振器产生的动应力的幅值与残余应力之和应稍大于机床床身的屈服强度,而动应力的值应小于疲劳极限。 % |7 u7 P5 l/ x+ ]2 r$ q# i) Z: {/ Q* r
2 Q. N0 s4 p& u- x0 T+ }& @' m
6 u* i0 h0 d3 q: j( A4 w+ | 3 结束语
( [7 u" j" @- E 利用振动时效消除机床床身铸件残余应力长期实践表明,振动时效能有效地消除和均化机床床身的残余应力,并取得明显的效果;振动时效工艺大大缩短了机床床身的制造时间,提高了生产效率和经济效益,解决了制造过程的变形问题,提高了机械制造质量。 5 ]! ^% s# R, E" m5 J( `+ k
! V4 S6 V/ S0 R( ?0 o |
本帖子中包含更多资源
您需要 登录 才可以下载或查看,没有帐号?注册会员
x
|