搅拌器在进行熔融玻璃搅拌时,受力情况较为复杂,无法直接估算。当我们对搅拌器的结构强度进行分析时,施加边界条件就比较困难。因此,我们采用耦合分析的来解决这个问题。 因为玻璃熔融状态下,是一种流体状态。因此,我们首先使用SolidWorksFlow Simulation进行流场分析获得搅拌器上的受力情况。然后,我们利用SolidWorks FlowSimulation与SolidWorksSimulation之间的接口,将流场计算得到的受力条件导出来作为边界条件,对搅拌器进行结构强度分析。先后进行了三个个设计方案的横向对比。列表如下: 方案1 搅拌器采用菱形截面的型材 壁厚2mm 7.970 Kg 方案2 搅拌器采用圆形截面的型材 壁厚2mm 7.917 Kg 方案3 搅拌器采用圆形截面的型材 壁厚1.5mm 7.662 Kg 我们对两种搅拌结构进行了流场分析和结构强度分析,并对比了两者之间的区别。从对比结果看,在给定的条件下,为圆形截面搅拌器应力水平更低,因此,我们接下来针对这种结构,减薄了壁厚,再次进行强度分析。并对比了壁厚调整前后的应力水平。 熔融玻璃的流场分析,目前的研究进展一般假设玻璃液为均质牛顿型粘性流体  ,同时,搅拌过程中玻璃液的温度基本不变,因此,我们考虑采用的等效玻璃液参数为:密度2200Kg/M3,动力粘度150Pa.s。 方案一采用菱形截面的搅拌器。我们首先对其进行了流场分析。流场分析的模型如下图所示: 1 J3 f5 \$ X4 K* ]
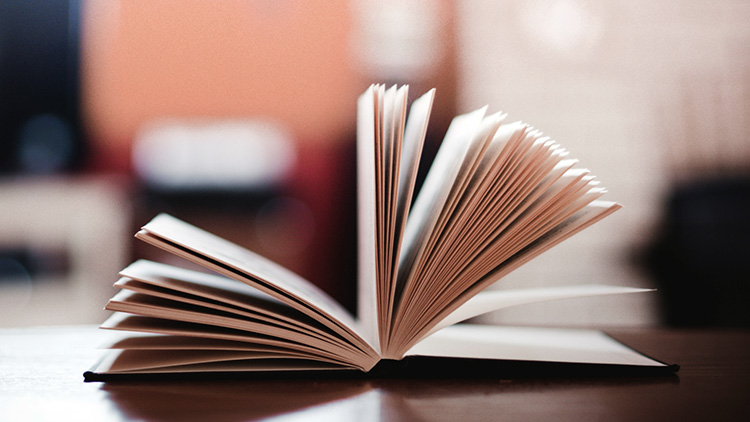 在流场分析时,我们给定坩埚中充满了玻璃液,并设定搅拌器的转速为45rpm,进行分析计算。计算得到的流场流线图如下图所示。 ; s1 u/ O3 h ?+ r5 H" w; ~
搅拌器上的承受的压力分布图如下图所示: 9 ?0 L) o8 `8 D; j! f
从流场分析的结果中我们还可以输出给定条件下,搅拌器上承受的扭矩,如下表: 通过流场分析,我们能够直接将流体分析的结果导出到SolidWorks Simulation中,作为边界条件,对搅拌结构进行结构强度分析。 之后,我们可以建立针对搅拌器的结构分析算例,在其中,我们只需设定相应的边界条件,然后即可划分网格并进行仿真了。在材料数据方面,我们得到了铂金高温下的机械性能,因此,采用高温铂金的材料特性数据进行本次计算。从结果对比的角度,只要几个设计方案的材料数据都取为一致,这样做出来的对比结果还是有意义的。我们使用的材料数据如下: ( F- v% n, l4 s& p, Z$ t
Pt 密度(g/cm3,20℃) 21.45 比热[J/(kg·K),20℃] 131.2 导热率[W/(m·K),0~100℃] 73 线膨胀系数(K-1×10-4) 9.1 弹性模量(N/mm2) 1.72×105 泊松比 0.39 为了获得较好的结果,我们采用3mm的单元大小进行网格划分。共划分单元122294个,局部网格单元如下图所示: 通过计算,我们得到了菱形截面搅拌器上的结构应力及位移结果。最大应力出现在菱形型材与圆柱相交的位置,大小为40.2Mpa,但考虑到此处为理想尖角位置,存在应力奇异,因此此处的应力是偏高且不收敛的,实际的应力犹豫存在焊缝过渡,应力水平应该低一些。另外,在搅拌框形结构上方,存在应力梯度较大的位置,此处的应力约为16MPa左右。在1300度高温的情况下,铂金屈服强度39.5MPa。因此,在给定条件下,方案1搅拌器整体还是安全的。局部可能接近屈服。 下图显示了变形结果。搅拌器在给定条件下,产生弯曲与扭转相结合的变形,其中,搅拌器扭转变形图如下图所示:由于搅拌器框形部分受到玻璃熔液的约束作用,变形较小,最大扭转出现在搅拌轴顶端。 4.2 方案2分析结果方案2的搅拌器结构基本不变,只是将菱形截面换成了圆形截面,壁厚2mm。这种方案的重量和方案1相比重量轻了53克,重量基本相同。我们仍然首先对其进行了流场分析,玻璃液的参数与上面所述相同。流场分析的结果如下图所示:
. O' z) M* K8 s+ G) y: Y; M( i3 p从流场的分布图来看,圆形截面的搅拌器,表面压力分布更为集中,流线分布显示速度的均匀性稍差。从扭矩情况看,方案2受扭矩与方案1基本一致。 采用同样的技术,我们将流场分析的结果导出到Simualtion中,对方案2进行了结构分析。 我们采用4mm的单元大小,总共划分了55683个单元,局部网格图如下图所示: 方案2的应力分布情况表明,最大应力出现在搅拌器框形与轴的交汇处,应力为28.3mm。但此处为理想尖角位置,存在应力奇异现象,实际应力应当偏低。而搅拌器框形上方出现应力梯度较大位置,此处应力约为14MPa左右。 变形分布云图如下图所示,变形趋势与方案1是类似的,最大扭转出现在搅拌器上端。 考虑1300度高温时,铂金的屈服强度为39.5MPa,方案2搅拌器整体是安全的。 4.3 方案3分析结果通过方案2的计算,我们可以得出结论,在给定条件下,方案2结构强度和刚度比方案1稍好。并且还有一定的安全裕量。因此,我们考虑是否能够通过减薄圆形截面壁厚,来减少贵金属的使用量。 基于这种考虑,我们将方案2的圆形截面壁厚减薄到1.5mm,并按照同样的条件进行结构有限元计算,并将结果与方案2进行对比。由于方案3的外形尺寸与方案2完全一致,因此,流场计算的结果就可以通用,不需要再计算了。 由于壁厚减薄,为了获得精确结果,我们采用2mm单元大小进行网格划分,共得到单元数量357723个,局部的网格图如下: 计算得到的应力结果表明,最高应力有所上升,但仍然在安全范围内。最大应力仍然出现在搅拌框与轴交界处,搅拌框上部同样出现应力梯度较大区域,改区域的应力约为14~16MPa。 从变形结果来看,壁厚减薄之后,扭转变形略有上升。最大变形量约为0.58mm。 5 结论通过上面的讨论,我们可以得出结论,在给定条件下,菱形截面的搅拌器强度和刚度稍弱,圆形截面的搅拌器强度和刚度较好。在壁厚减薄之后,圆形截面的搅拌器仍然比菱形截面的搅拌器要好。我们将对比结果列表如下:$ q- \5 f- O5 G; c' K) T
1 r9 A& L3 F6 X2 a9 Z. q
方案 结构描述 壁厚 最大应力 质量 方案1 搅拌器采用菱形截面的型材 壁厚2mm 40.2Mpa 7.970 Kg 方案2 搅拌器采用圆形截面的型材 壁厚2mm 28.3Mpa 7.917 Kg 方案3 搅拌器采用圆形截面的型材 壁厚1.5mm 33.7Mpa 7.662 Kg ' [$ }$ l& H5 D) w0 M) C D* M
通过对比,我们认为在给定条件下,圆形截面的搅拌器强度和刚度相对更好。 |