近年来,随着工业的发展,机械自动化程度不断在提高,标准件大批量生产都有想配套的设备和较为成熟的工艺,相对的非标异型件对单件和小批量生产还是可以采用四爪卡盘进行装夹,但车削加工有一定难度。实际生产中如果遇上大批量生产的零件,则需要采取一些相应的技术措施,如设计专用夹具、改进刀具和加工方法等解决生产中遇到的问题,使其在批量生产中发挥最大的作用。 - |! d, U' A- |
; p; ]6 A; j% D* [1 U 一、异形件工艺分析+ v( L* b$ k( L# A' f' l) P1 ~
异形件如图1所示,材料选择为黄铜(HMn58-2),中批量生产。工序主要在车床加工,要求有:φ23.5mm内孔,倒角C2,总长223.5±0.5mm,并保证φ23.5mm的内孔与φ40的孔同轴度0.25。其余表面均在上道序加工完毕,总长有4mm余量。先使用的设备为CA6140普通车床。 7 \) p+ x% h1 v# A1 u; h, W1 W
二、车床专用夹具使用分析
0 t6 i7 Q" S5 e3 N4 {& m! W在CA6140普通车床上加工,利用专用夹具(如图2所示)进行装夹以提高效率。加工工序是夹具板安装在四爪卡盘上,并校正,然后将工件大面贴在夹具板上,然后分别用两组M12螺栓和M12的螺母通过工件上φ12.5的孔,将工件连接并夹紧在夹具板上。其加工走刀路线如图3所示。 . R g' \2 l$ r
" f- m' C" g. F 三、存在问题分析- T1 U" T( d2 n
在产品改进前按照上诉方案加工,经批量加工后发现两个问题: (1)φ23.5mm的内孔与φ40的孔同轴度无法保证。这里所使用的夹具形状为板快状,安装时将工件的大侧面帖在夹具板上,下侧面有两颗M6的螺栓定位,左侧面有一颗M6螺钉定位。从定位原理上分析,这套夹具构成六点定位原理,限制工件的六个自由度。先分析工件在夹具中的定位误差,由图一可知,φ23.5的内孔的工艺基准为φ40的外圆,因此定位中就产生了基准不重合误差,如图4所示。
: @; G/ A$ T O+ y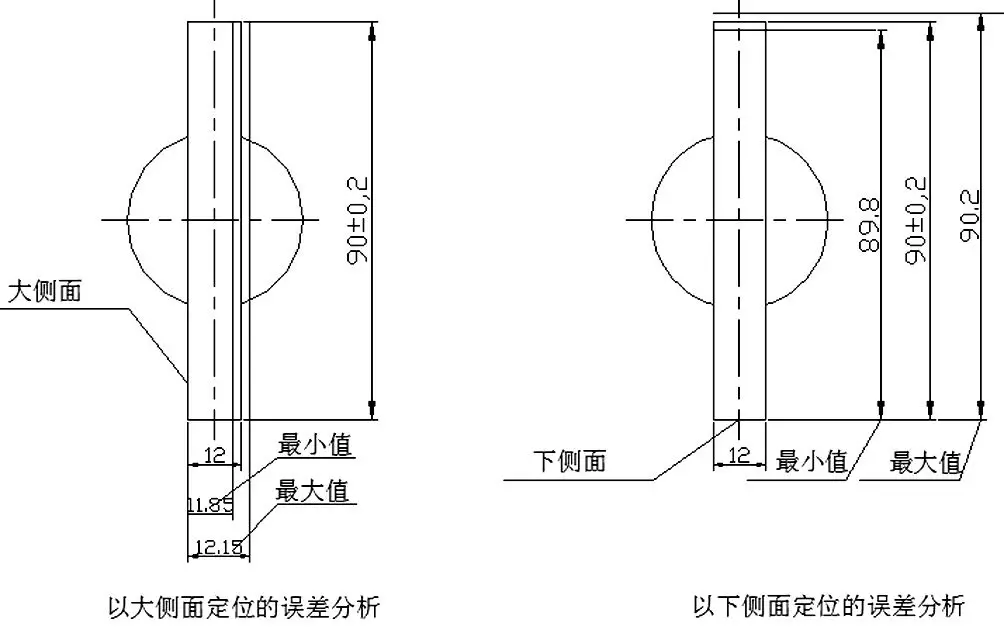 以大侧面定位时,夹具的定位基准在大侧面上,与φ40的外圆的轴心线存在尺寸公差问题,△d1=(12.15-11.85)/2=0.15mm,同理,以下侧面定位过程中也存在着同样的问题,△d2=(90.2-89.8)/2=0.2mm,T1和T2将会被代入本工序中来。 根据定位误差的使用要求,一般的有公式:△d≤(1/5~1/3)*T (T为工序公差)就是同轴度0.25mm,则△d≤(1/5~1/3)*0.25=0.05mm~0.083mm,也就是说△d最大只能在0.083mm,而本列中仅△d1=0.15mm这一项就大大超过使用要求,并且在没有分析夹具安装误差、夹具的对定误差、加工过程误差,所以说在加工过成中同轴度要求将无法批量保证。 (2)加工效率较低,零件车加工时,端面车两刀至尺寸用时25s,因内孔尺寸公差较大,有0.16mm,可以用φ23.5的钻头一次打出,用时20s。倒角C2,用时8s。工件采用两颗M12的螺栓手工连接并紧固,用时较长50s,那么单件总用时1分43秒,可以说装夹时间占加工用时一半时间,而且劳动强度大,故加工效率低,每班只能生产200件左右。
) Q, H+ p3 U4 }' i 四、设备、夹具的工艺改进& K! c( E3 |# @) x. V2 c
以上两个问题有一个共同点,都与夹具的设计结构有关,因工件在夹具中的定位误差超差造成同轴度不能批量保证,因夹紧采用手工螺旋夹紧而用时较长,造成加工效率低。为了解决上诉两个问题,需要对夹具的结构进行改造,并采用了一套新的加工方案,如图5所示。 夹具方面采用了长卡爪直接夹在工件φ40的外圆上,又采用了液压卡盘,实现自动夹紧、松开。设备方面更换成CK6140型数控车床。 较之普通车床,采用数控车床有以下的优点: (1)加工对象的适应性强; (2)加工精度高; (3)生产效率高,劳动强度低; (4)自动化程度高; (5)良好的经济效益; (6)有利于生产管理的现代化; (7)完全适应中小批量加工。 改进后,因长卡爪直接夹在工件的外圆上,定位基准和工艺基准重合,那么基准不重合误差为零,所以同轴度可以批量保证。 数控车床搭配液压卡盘使装夹实现全自动化,也使之减小了装夹时间,由原来的50S减少到15S。 这里要注意的是,钻头也可以装夹在刀架上,给钻头做一个夹具(如图6所示),加工过程中刀架自动走刀。走刀时间由原来的53s减少到40s,这样加起来也就55s,单件加工比原来减少到47s,约一倍时间。至此,每班生产件数有原来的200件提高到350件左右,这样使上文的两个问题都能得到解决。 在数控车上进行上述零件的加工,不仅自动化程度更高,而且夹具的作用也得到更加充分的发挥。对于加工复杂的异形零件,所采用的夹具和加工方案,也都是在加工过程中不断摸索。 |