如果零件既要求表面有较高的硬度和耐磨性,又要求心部具有足够的韧性,必须采用各种表面强化工艺。 一、表面热处理1、表面淬火 表面淬火是指在不改变钢的化学成分及心部组织情况下,利用快速加热将表层奥氏体化后进行淬火以强化零件表面的热处理方法。 7 b1 W4 C5 v# h5 ?* i
/ U0 \ D5 ~, F T0 V1.1表面淬火目的: ① 使表面具有高的硬度、耐磨性和疲劳极限; ② 心部在保持一定的强度、硬度的条件下,具有足够的塑性和韧性。即表硬里韧。 适用于承受弯曲、扭转、摩擦和冲击的零件。 8 a/ ^! |1 z5 {' |8 b, b
8 d% }9 z( x" f* k# [2 E1.2表面淬火用材料 ⑴ 0.4-0.5%C的中碳钢。含碳量过低,则表面硬度、耐磨性下降。含碳量过高,心部韧性下降; ⑵ 铸铁 ,提高其表面耐磨性。 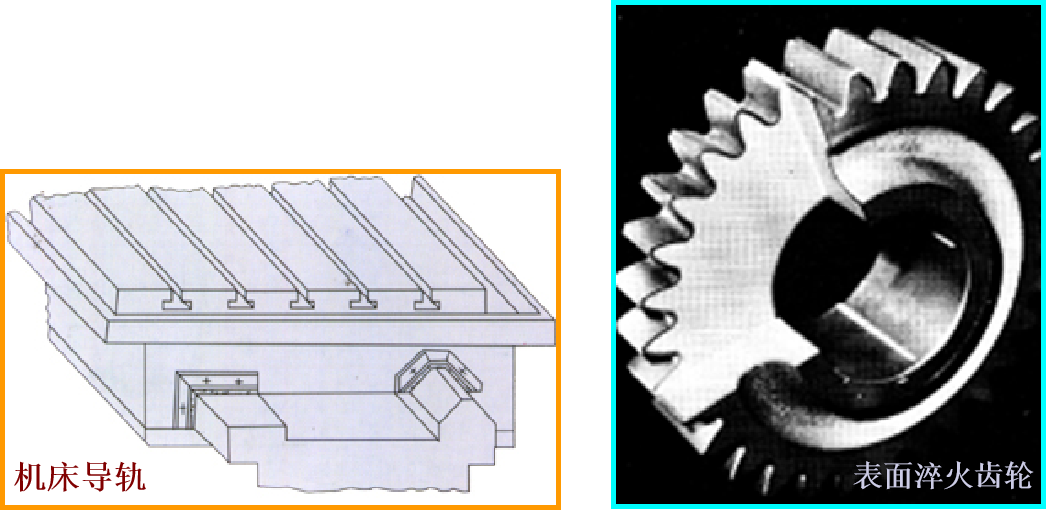
3 G( F4 Q& C$ o6 J3 w u$ F& x7 x" Y3 c& i# X
1.3预备热处理 ⑴工艺:对于结构钢为调质或正火。前者性能高,用于要求高的重要件,后者用于要求不高的普通件。 ⑵目的:为表面淬火作组织准备;获得最终心部组织。 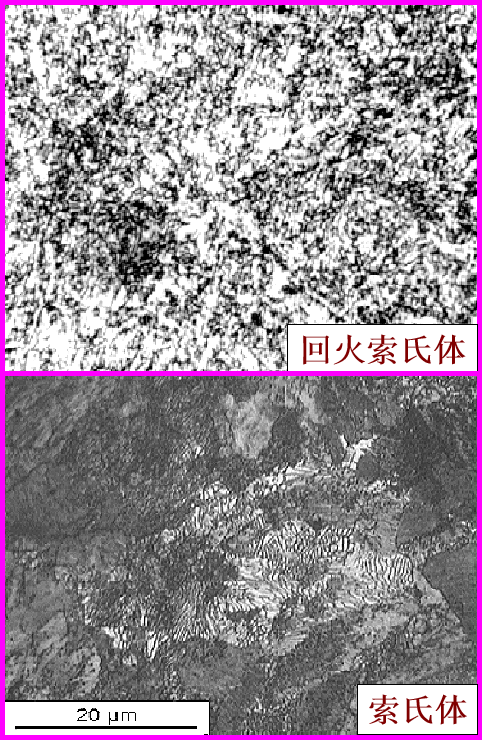
7 x% p( [ n; k) `8 i) P% K) m- j% @9 n2 ?* O9 r
表面淬火后的回火,采用低温回火,温度不高于200℃。回火目的为降低内应力,保留淬火高硬度、耐磨性。 表面淬火+低温回火后的组织:表层组织为M回;心部组织为S回(调质)或F+S(正火)。 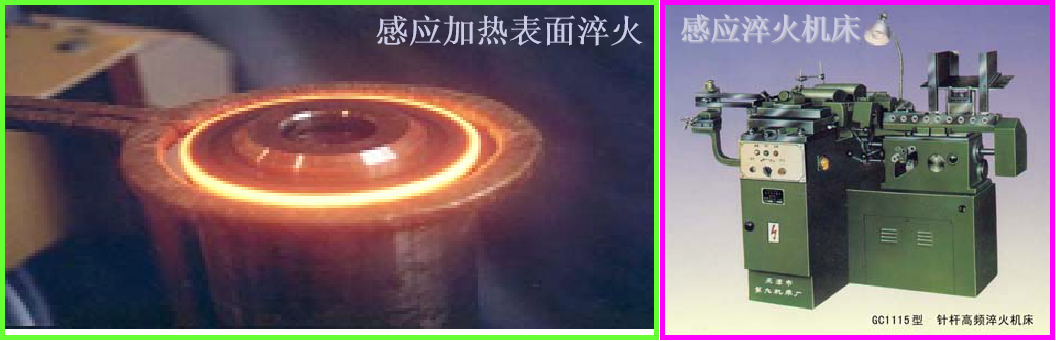
- x" \! S) l8 Y3 [3 B0 [3 d6 J( P/ O6 C
1.4表面淬火常用加热方法 ⑴ 感应加热: 利用交变电流在工件表面感应巨大涡流,使工件表面迅速加热的方法。 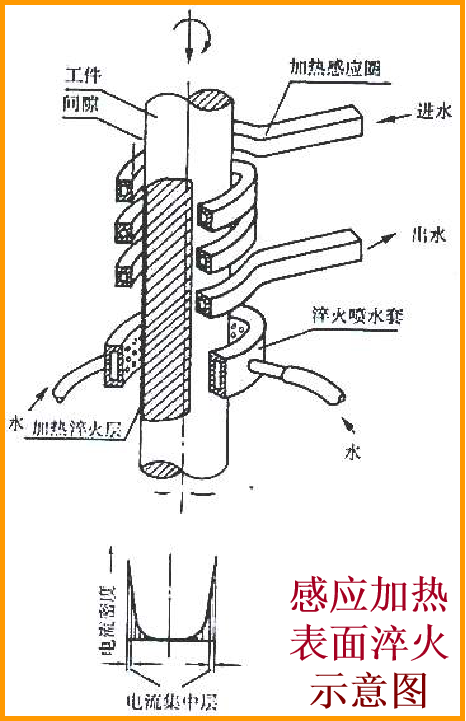
+ e% y1 _ s @) b3 g2 Y
6 `0 E1 g3 T F) a% M+ T, m6 a+ g感应加热分为: 高频感应加热:频率为250-300KHz,淬硬层深度0.5-2mm 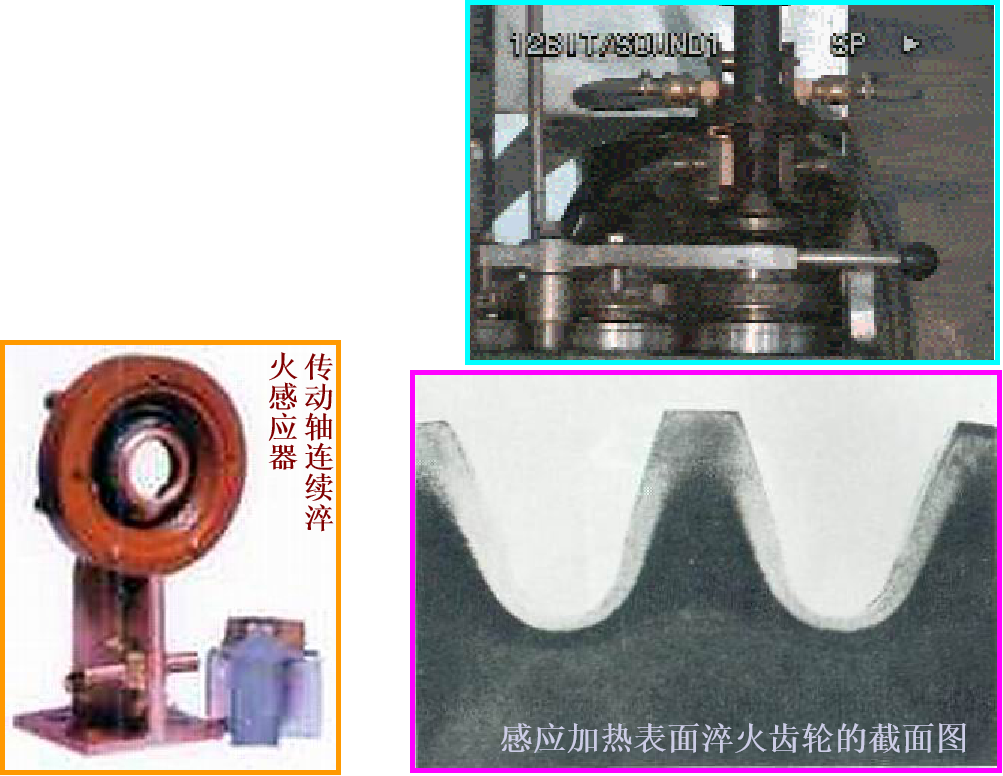
% K l, \$ F/ O5 k5 `* f4 _& c- ^+ D! \2 c! v. f d. _% W
中频感应加热:频率为2500-8000Hz,淬硬层深度2-10mm。 2 c# {+ I; v( X/ h
6 t- }+ K& g/ n0 w6 g& G
工频感应加热:频率为50Hz,淬硬层深度10-15 mm 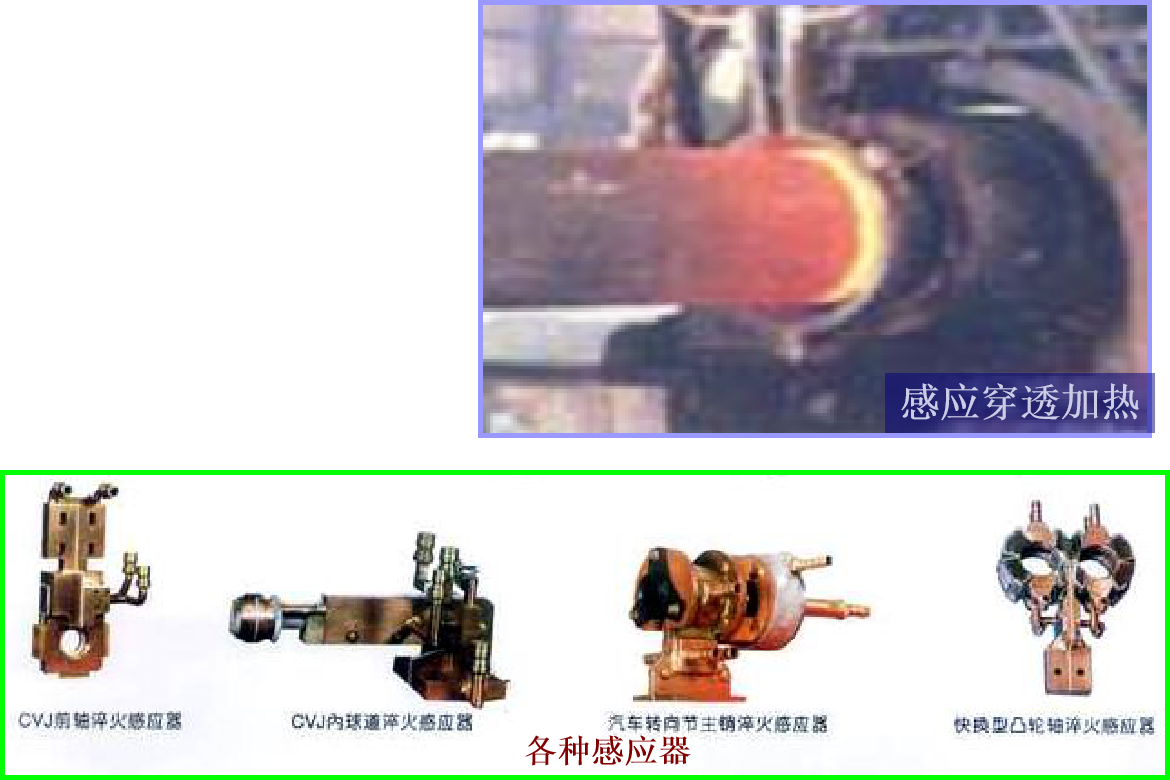
3 z w# X; E! @& I7 j" o% v2 `3 p7 J5 l% _6 ?
⑵ 火焰加热: 利用乙炔火焰直接加热工件表面的方法。成本低,但质量不易控制。 ⑶ 激光热处理: 利用高能量密度的激光对工件表面进行加热的方法。效率高,质量好。 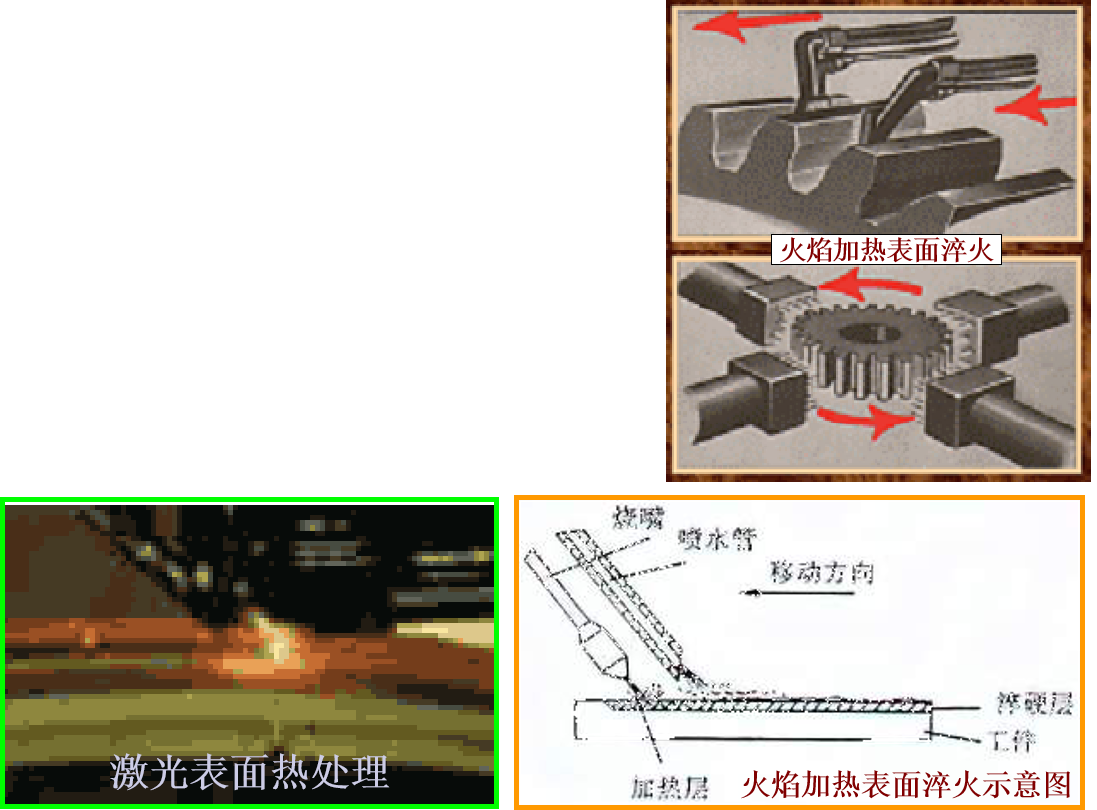
4 I% S- [* T9 o+ b9 }- U$ O/ W( J3 [3 w. ~$ i7 @7 I# s
2、化学表面热处理 化学热处理是将工件置于特定介质中加热保温,使介质中活性原子渗入工件表层从而改变工件表层化学成分和组织,进而改变其性能的热处理工艺。 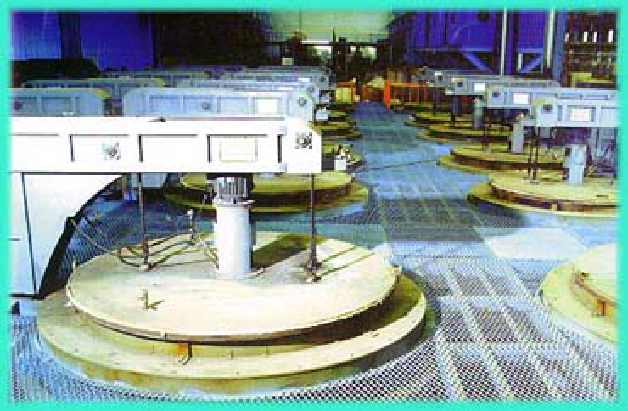
: ]3 a. o( `) b5 [$ ?0 v+ ?) U0 G+ D/ u; ?% P+ c
与表面淬火相比,化学热处理不仅改变钢的表层组织,还改变其化学成分。化学热处理也是获得表硬里韧性能的方法之一。 根据渗入的元素不同,化学热处理可分为渗碳、氮化、多元共渗、渗其他元素等。 4 [6 s# _* j% Y" s% h- b! o# F
+ y: X8 K' l" ], e常用的化学热处理: 渗碳、渗氮(俗称氮化)、碳氮共渗(俗称氰化和软氮化)等。 渗硫、渗硼、渗铝、渗钒、渗铬等。发兰、磷化可以归为表面处理,不属于化学热处理。 化学热处理过程包括分解、吸收、扩散三个基本过程。 ①化学热处理的基本过程 ⑴介质(渗剂)的分解: 分解的同时释放出活性原子。如:渗碳 CH4→2H2+[C],氮化 2NH3→3H2+2[N] ⑵工件表面的吸收: 活性原子向固溶体溶解或与钢中某些元素形成化合物。 ⑶原子向内部扩散。 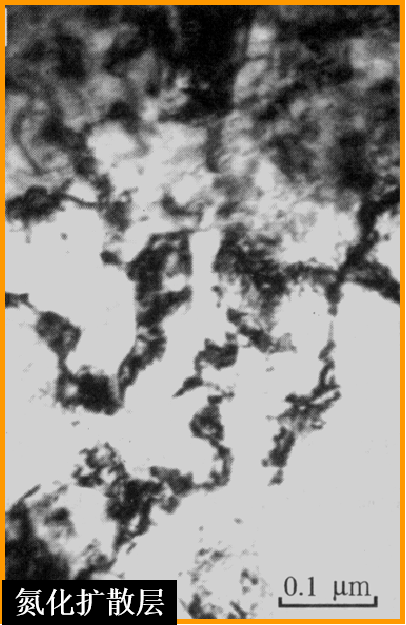
. S' E9 W6 Z9 V; N! T {- k' j
+ X; l% S* Z+ n+ F②钢的渗碳是指向钢的表面渗入碳原子的过程。 ⑴渗碳目的:提高工件表面硬度、耐磨性及疲劳强度,同时保持心部良好的韧性。 ⑵渗碳用钢:为含0.1-0.25%C的低碳钢。碳高则心部韧性降低。 7 @' w" z f5 d: P
, U. { t5 i# S" ]1 c7 [' b! U
③渗碳方法 ⑴ 气体渗碳法:将工件放入密封炉内,在高温渗碳气氛中渗碳。渗剂为气体 (煤气、液化气等)或有机液体(煤油、甲醇等)。优点: 质量好, 效率高;缺点: 渗层成分与深度不易控制 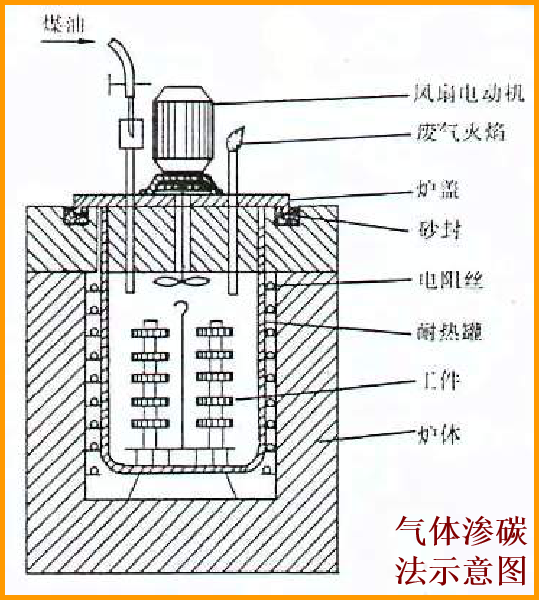
" R4 F/ q: }6 m M6 t1 d D, Y
' s6 [# j) j l% h( w1 m' t⑵ 固体渗碳法:将工件埋入渗剂中,装箱密封后在高温下加热渗碳。渗剂为木炭。优点:操作简单;缺点:渗速慢,劳动条件差。 ⑶ 真空渗碳法:将工件放入真空渗碳炉中,抽真空后通入渗碳气体加热渗碳。优点: 表面质量好, 渗碳速度快。 $ U; \9 t, P8 z) W |% Z' g
1 Q- {+ z: N" s d; s# x) _
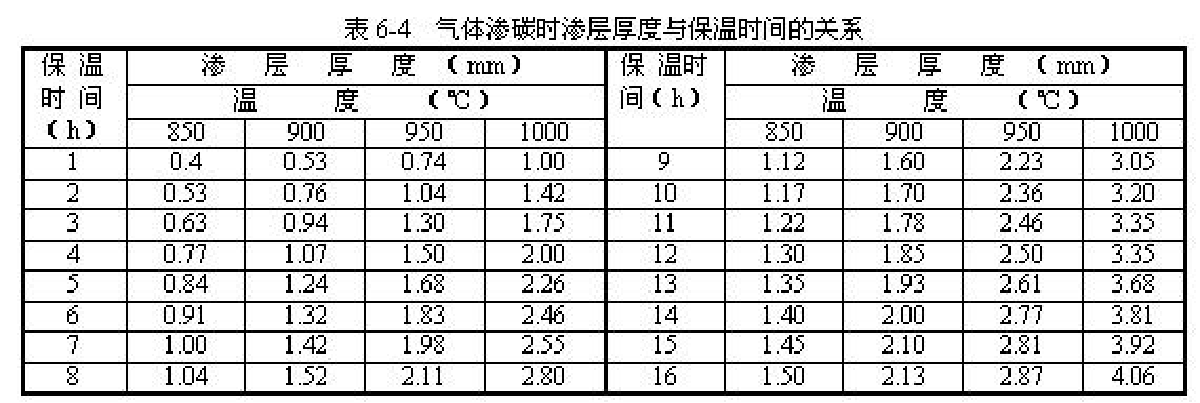
" @7 k$ q* r4 k6 M
2 y, `4 u* ?% G, k" V+ W8 z" o# O4 n④渗碳温度:为900-950℃。渗碳层厚度(由表面到过度层一半处的厚度):一般为0.5-2mm。 渗碳层表面含碳量:以0.85-1. 05为最好。渗碳缓冷后组织:表层为P+网状Fe3CⅡ; 心部为F+P; 中间为过渡区。 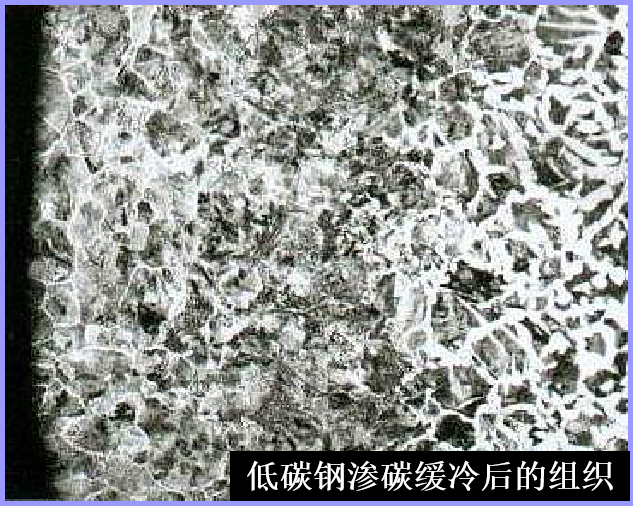
9 H& |/ ]9 |9 ^, J! Q* C- |7 W \' p! b! Z2 d
⑤渗碳后的热处理:淬火+低温回火, 回火温度为160-180℃。淬火方法有: ⑴ 预冷淬火法 渗碳后预冷到略高于Ar1温度直接淬火。 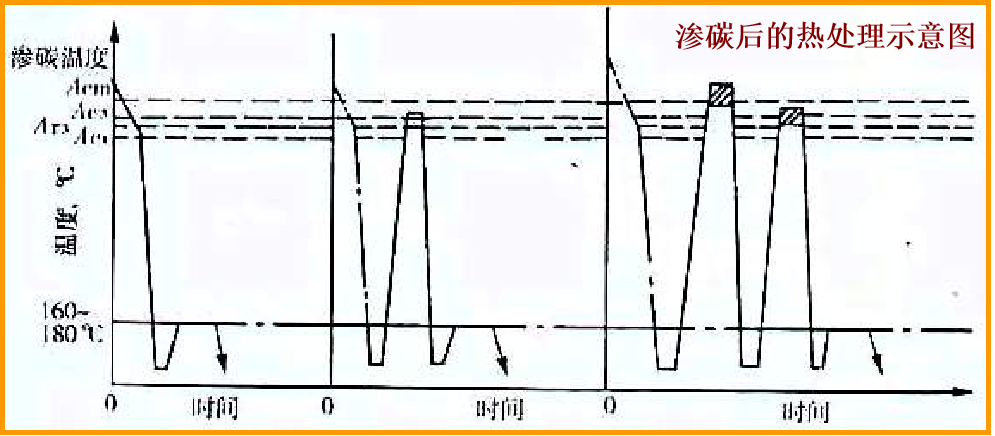
0 I; V) N3 L- F1 I3 s# M M$ n; w! h, {3 h& A! f
⑵一次淬火法:即渗碳缓冷后重新加热淬火。 ⑶ 二次淬火法:即渗碳缓冷后第一次加热为心部Ac3+30-50℃,细化心部;第二次加热为Ac1+30-50℃,细化表层。 9 f3 t3 H# ?; m
1 [4 T& w4 b! [! |常用方法是渗碳缓冷后,重新加热到Ac1+30-50℃淬火+低温回火。此时组织为: 表层:M回+颗粒状碳化物+A’(少量) 心部:M回+F(淬透时) 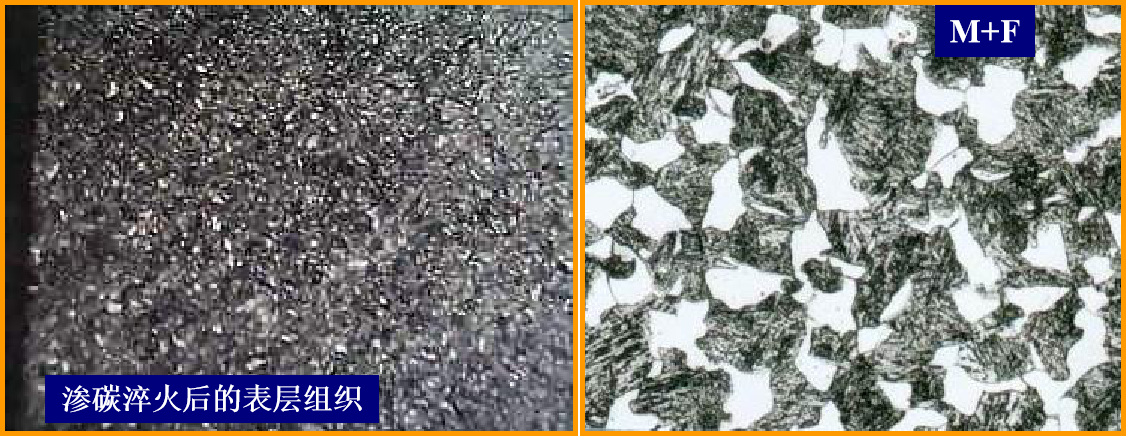
& o( w4 Y9 w P5 p' C5 D& k# t
2 x' ~# _4 V' u7 C7 Q⑥钢的氮化:氮化是指向钢的表面渗入氮原子的过程。 ⑴氮化用钢,为含Cr、Mo、Al、Ti、V的中碳钢。常用钢号为38CrMoAl。 ⑵氮化温度为500-570℃。氮化层厚度不超过0.6-0.7mm。 # x+ G3 V# Y+ f- O! n
0 h! C0 ]. l* I9 k. a0 `4 c常用氮化方法:气体氮化法与离子氮化法。 气体氮化法与气体渗碳法类似,渗剂为氨。离子氮化法是在电场作用下,使电离的氮离子高速冲击作为阴极的工件。与气体氮化相比,氮化时间短,氮化层脆性小。 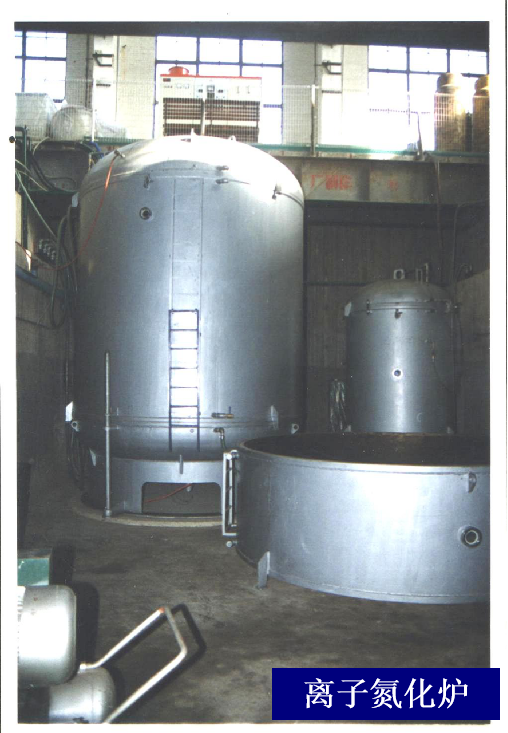
7 c! F1 [5 H/ p, ~. Y* f% A+ n% L- T; A( L
⑷氮化的特点及应用 氮化件表面硬度高(69~72HRC),耐磨性高。 疲劳强度高。由于表面存在压应力。 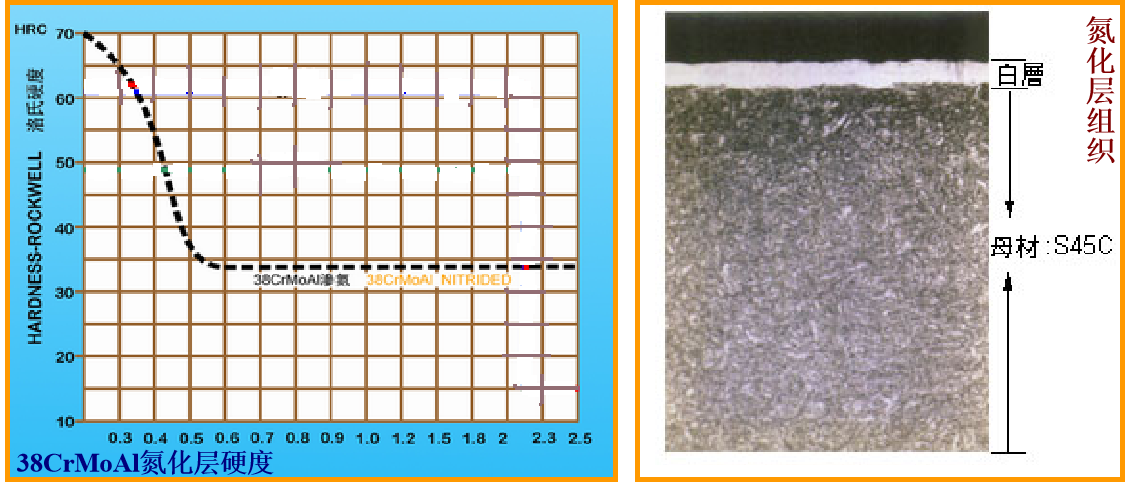
Z3 h: ~6 ]# G/ B# |
$ E) O% X$ H* w( ?8 M& W0 B) W工件变形小。原因是氮化温度低,氮化后不需进行热处理。 耐蚀性好。因为表层形成的氮化物化学稳定性高。 氮化的缺点:工艺复杂,成本高,氮化层薄。 用于耐磨性、精度要求高的零件及耐热、耐磨及耐蚀件。如仪表的小轴、轻载齿轮及重要的曲轴等。 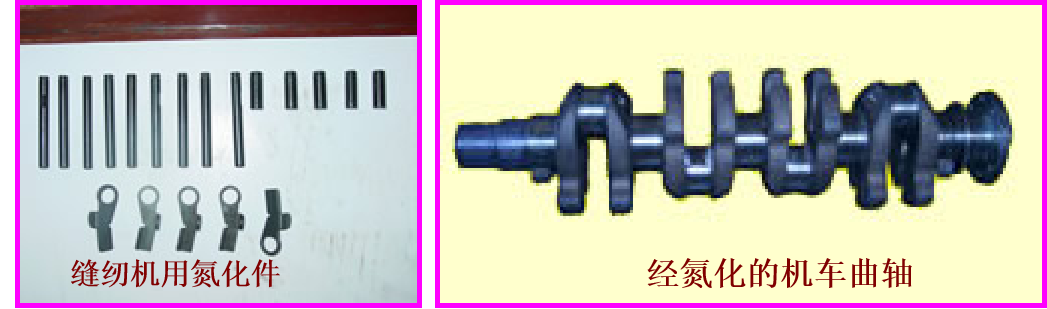
! w5 d. n3 `2 W+ m; [8 c
1 U& I3 T2 r3 I1 _3 X% B滲氮与滲碳相比:滲氮层硬度和耐磨性高于滲碳层,硬度可达69~72HRC,且在600~650℃高温下仍能保持较高硬度;滲氮层具有很高的抗疲劳性和耐蚀性;滲氮后不需再进行热处理,可避免热处理带来的变形和其他缺陷;滲氮温度较低。只适用于中碳合金钢,需要较长的工艺时间才能达到要求的滲氮层。 二、表面形变强化表面形变强化指使钢件在常温下发生塑性变形,以提高其表面硬度并产生有利的残余压应力分布的表面强化工艺。工艺简单,成本低廉,是提高钢件抗疲劳能力,延长其使用寿命的重要工艺措施。 1、喷丸 喷丸强化是将大量高速运动的弹丸喷射到零件表面上,犹如无数个小锤锤击金属表面,使零件表层和次表层发生一定的塑性变形而实现强化的一种技术。 应用:形状较复杂的零件。在磨削、电镀等工序后进行 2、滚压处理 利用自由旋转的淬火钢滚子对钢件的已加工表面进行滚压,使之产生塑性变形,压平钢件表面的粗糙凸峰,形成有利的残余压应力,从而提高工件的耐磨性和抗疲劳能力。 应用:圆柱面、锥面、平面等形状比较简单的零件 三、表面覆层强化表面覆层强化是通过物理或化学的方法在金属表面涂覆一层或多层其他金属或非金属的表面强化工艺。目的:提高钢件的耐磨性、耐蚀性、耐热性或进行表面装饰。 1、金属喷涂技术 将金属粉末加热至熔化或半熔化状态,用高压气流使其雾化并喷射于工件表面形成涂层的工艺称为热喷涂。利用热喷涂技术可改善材料的耐磨性、耐蚀性、耐热性及绝缘性等。 广泛用于包括航空航天、原子能、电子等尖端技术在内的几乎所有领域。 7 a( L- j* C2 g' U) L$ _: ?9 L
9 P* y4 J1 S& h! W2 p% T. w
2、金属镀层 在基体材料的表面覆上一层或多层金属镀层,可以显著改善其耐磨性、耐蚀性和耐热性,或获得其他特殊性能。电镀:工件作为阴极。化学镀:不外加电源的条件下,利用化学还原的方法在基体材料表面催化膜上沉积一层金属的表面强化方法。特点:形状工件复杂上也能得到均匀厚度镀层;镀层晶粒细小致密,孔隙与裂纹少;可以在非金属材料表面沉积金属层。 复合镀:电镀或化学镀的溶液中加入适量金属或非金属微粒,借助于强烈的搅拌,与基质金属一起均匀沉积而获得特殊性能镀层的表面强化方法。应用:对材料有特殊要求。原子能工业和航天航空工业 3、金属碳化物覆层~气相沉积法 气相沉积技术是指将含有沉积元素的气相物质,通过物理或化学的方法沉积在材料表面形成薄膜的一种新型镀膜技术。根据沉积过程的原理不同,气相沉积技术可分为物理气相沉积(PVD) 和化学气相沉积(CVD)两大类。 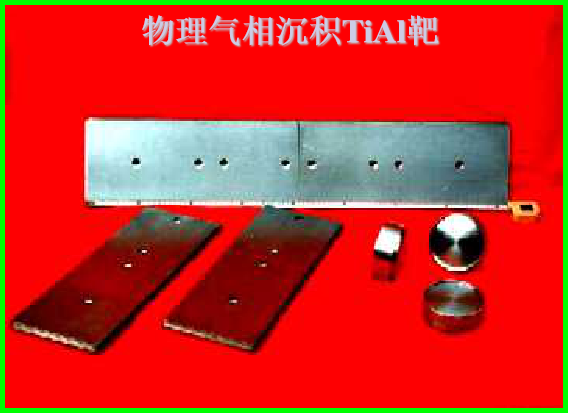
/ A2 H3 c8 E) P5 f5 e8 l
- E1 x8 R, J5 g7 d; Y/ E物理气相沉积(PVD) 物理气相沉积是指在真空条件下,用物理的方法,使材料汽化成原子、分子或电离成离子,并通过气相过程,在材料表面沉积一层薄膜的技术。 物理沉积技术主要包括真空蒸镀、溅射镀、离子镀三种基本方法。 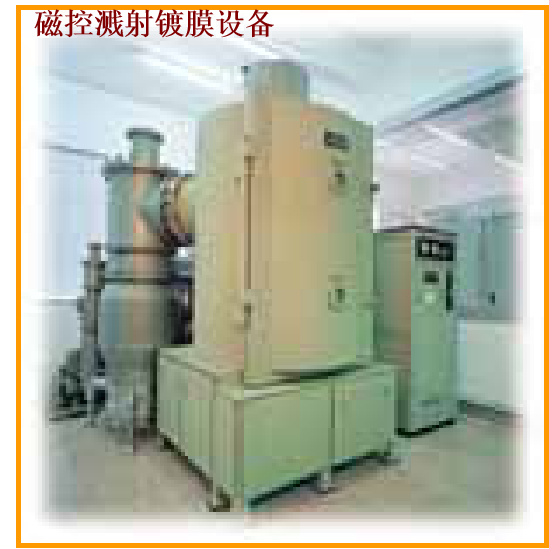
! W+ K+ g5 i" ]% p- ~9 l# q
! d! S/ _- r9 s. V% E" p真空蒸镀是蒸发成膜材料使其汽化或升华沉积到工件表面形成薄膜的方法。 8 U( ~* H! }1 ~" S/ r
9 w# A7 X) Y2 ^/ @# U) n溅射镀是在真空下通过辉光放电来电离氩气,氩离子在电场作用下加速轰击阴极,溅射下来的粒子沉积到工件表面成膜的方法。 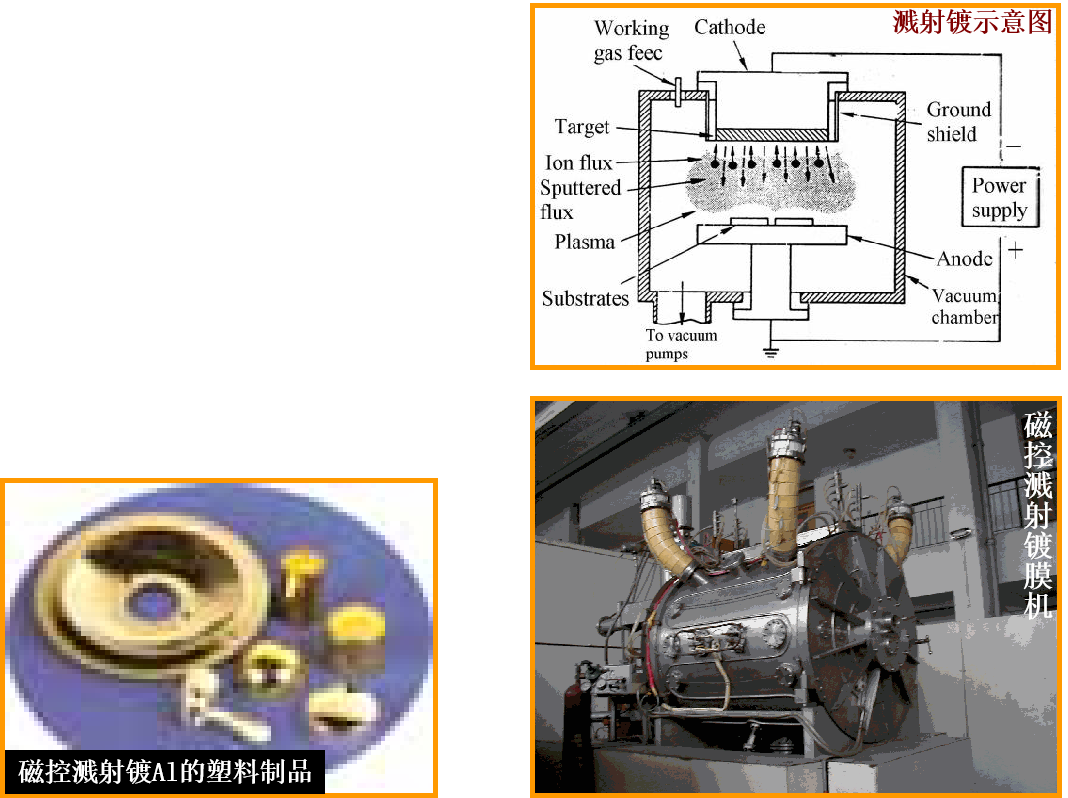
6 m% e' F F. x
4 C! \- X2 m0 T) x4 `& D% i离子镀是在真空下利用气体放电技术,将蒸发的原子部分电离成离子,与同时产生的大量高能中性粒子一起沉积到工件表面成膜的方法。 * x) W( B& Y+ j. p
6 B5 q0 i8 k; @: n) Z. `6 S
物理气相沉积具有适用的基体材料和膜层材料广泛;工艺简单、省材料、无污染;获得的膜层膜基附着力强、膜层厚度均匀、致密、针孔少等优点。广泛用于机械、航空航天、电子、光学和轻工业等领域制备耐磨、耐蚀、耐热、导电、绝缘、光学、磁性、压电、滑润、超导等薄膜。 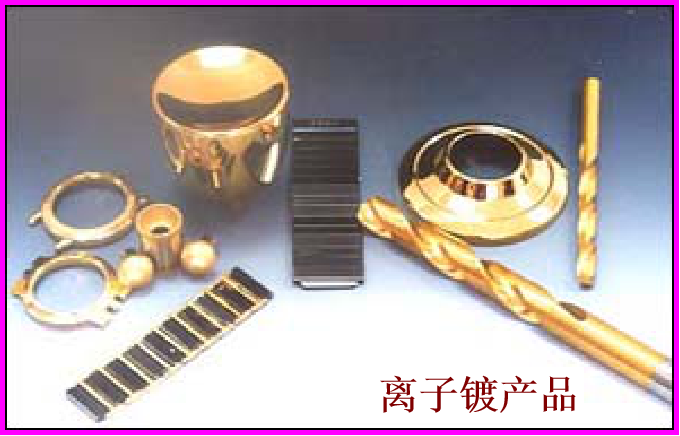
* \: X' F% c- A$ \
1 F3 @7 z9 K: j' A) K. ?②化学气相沉积(CVD) 化学气相沉积是指在一定温度下,混合气体与基体表面相互作用而在基体表面形成金属或化合物薄膜的方法。例如,气态的TiCl4与N2和H2在受热钢的表面反应生成TiN,并沉积在钢的表面形成耐磨抗蚀的沉积层。 Q8 I) H5 F. B" W
% e% B2 {. }$ _- g0 L+ g$ x
由于化学气相沉积膜层具有良好的耐磨性、耐蚀性、耐热性及电学、光学等特殊性能,已被广泛用于机械制造、航空航天、交通运输、煤化工等工业领域。 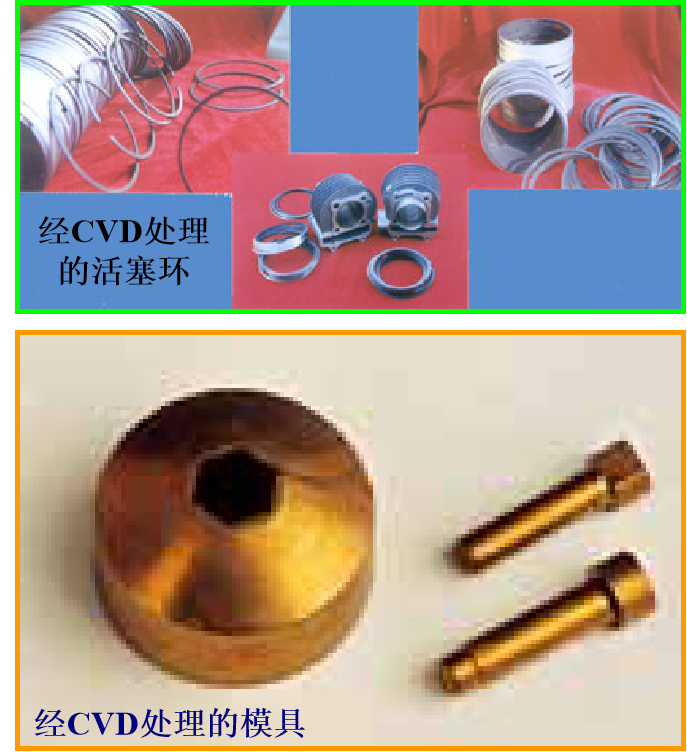
! l: j( v" Q* Q/ c& g* a2 N5 f+ Z% V7 k$ d4 L0 n# s/ G; h2 z4 D% P
四、热处理的工艺性热处理时机的确定:预备热处理一般安排在毛坯生产之后,切削加工之前 正火和退火:消除热加工时毛坯的内应力、细化晶粒、调整组织、改善切削加工性 调质:提高零件综合性能,为最终热处理做组织上的准备 最终热处理(淬火+回火或化学热处理):一般放在半精加工之后,磨削加工之前。 |